Introducing EXTRACTION GRADE™ nButane, Propane & Isobutane
Gas Innovations is the world leader in high purity hydrocarbon gases specializing in packaged gas for food, medical and electronics grade applications. We have used our decades of experience to develope the highest quality most consistant extraction solvent products available. Contact us to find a Gas Innovations approved distributor near you.
Extraction Grade testing standards: Certifications now listing BTEX, Alcohols (methanol) and heavy metals. Protect against fast crash (medusa stones) and contamination from impurities found in untreated products. Diamond Grade™ package now available.
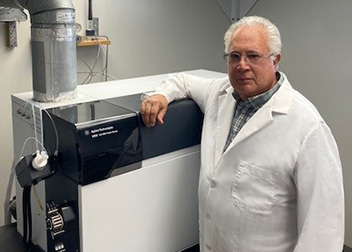
Lab Manager / Chemist - John Garcia. 23 years in hydrocarbon analysis, purification and developing methods.
Technical support directly from the source.
The first standards developed specifically for extraction
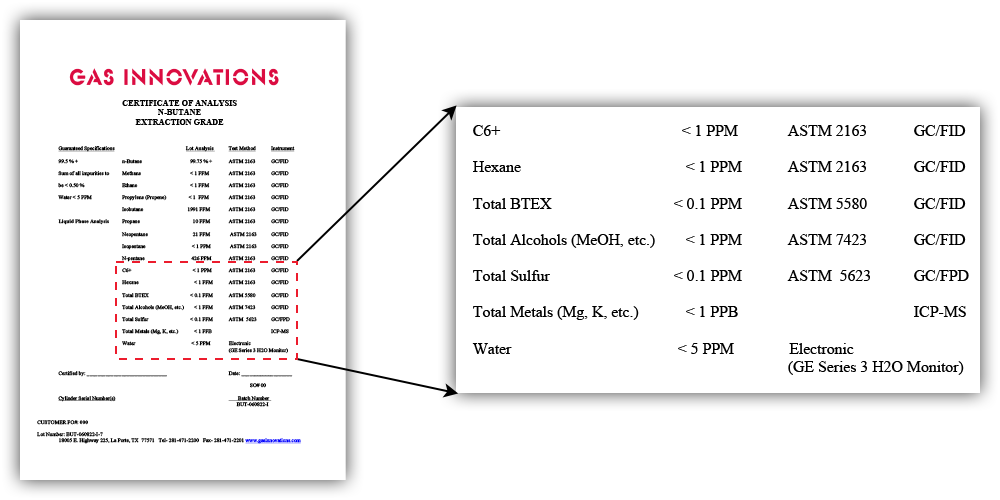
View EXTRACTION GRADE™ Products
Third Party Verified - GC Mass Spec
Extraction Solvents (Non-Odorized)
- Highest purity products available
- Dedicated lines, filters, pumps & hoses
- Solvents are pre distilled & ready for use
- We do not salvage residual product
- Specialized processes in place to ensure purity & eliminate potential contaminants
- State of the art onsite laboratory
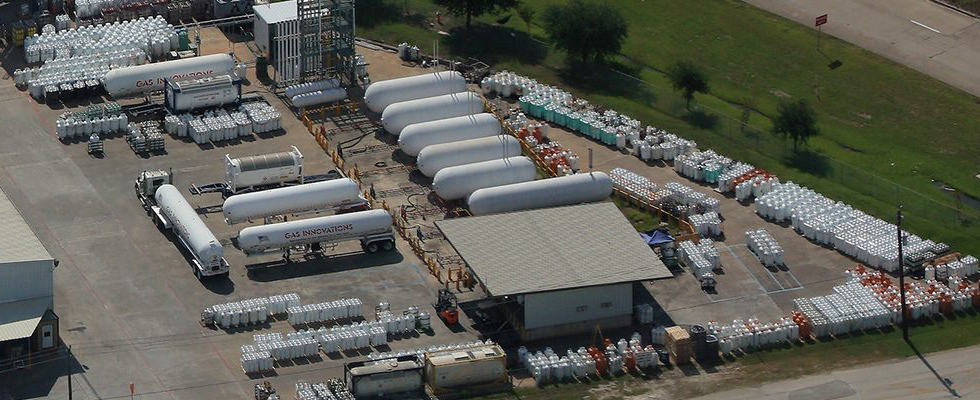
Maintain Purity From Start To Finish
1. Specialty Cylinder Packaging
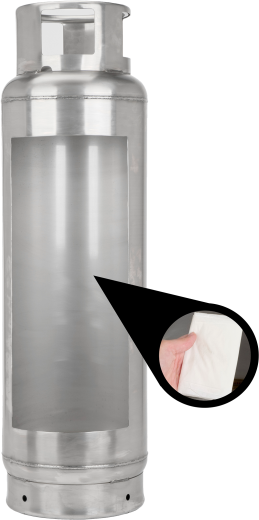
Diamond Grade™ - Stainless Steel:
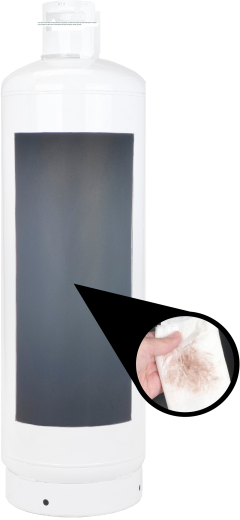
Extraction Grade™ - Carbon Steel:
* Carbon steel cylinders can break down over time introducing non-volatile residue (rust) and other contaminants.
2. Process Controls / Quality Standards
Competitors / Top Filling Refill Procedures:
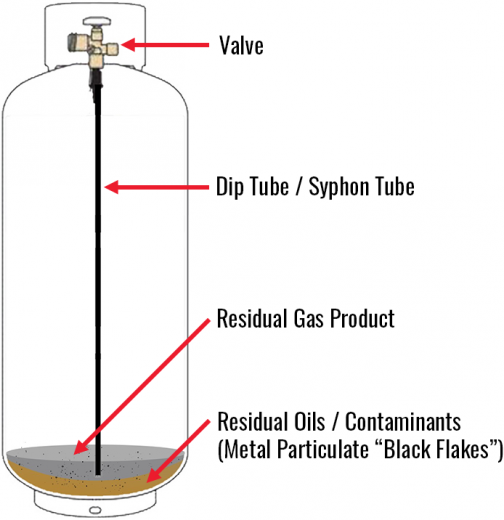
Top Filling – Filling gas product on top of residual gas & unknown contaminants.
Gas Innovations Refill Procedures:
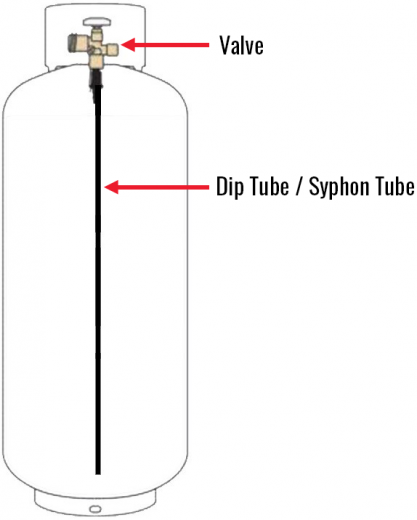
Evacuation - Residual product removed
Inspection - Internal wash if necessary
Vacuum - Remove air / moisture.
Fill - Max allowed by DOT.
Analysis - Certified product (COC).
Examples of residual oils / unknown contaminants. * Note a passive distillation may remove some solids but will not remove contaminants with similar chemical composition (ex. Benzene, Hexane).
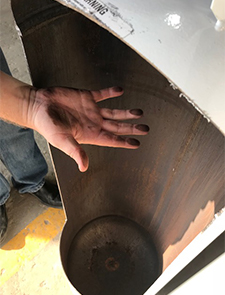
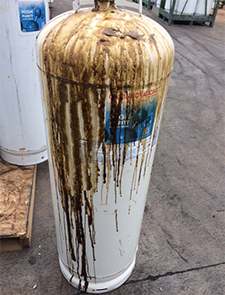
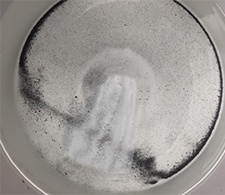
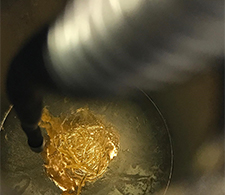
Cylinder Cleaning / Maintenance
(Slide < > R to L)
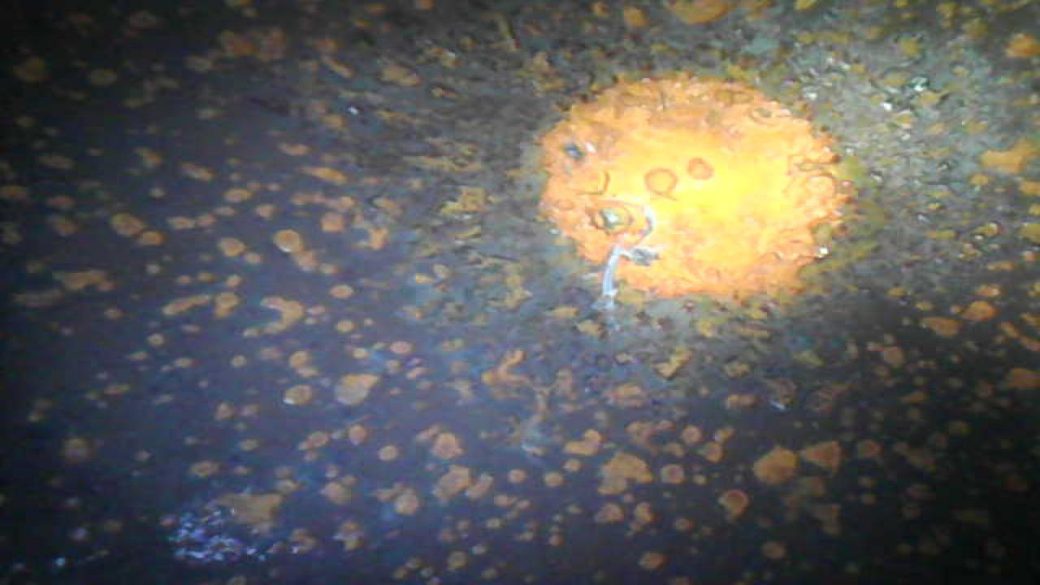
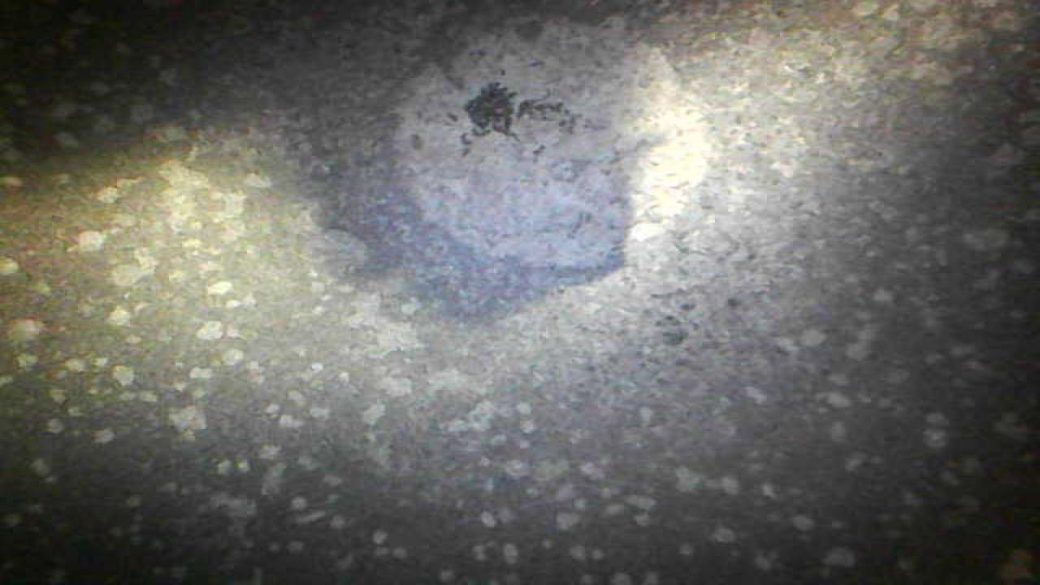
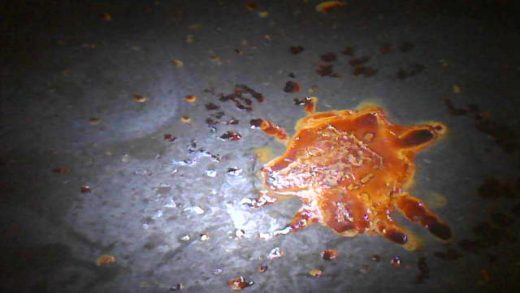
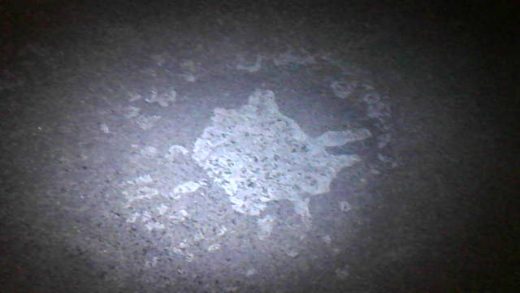
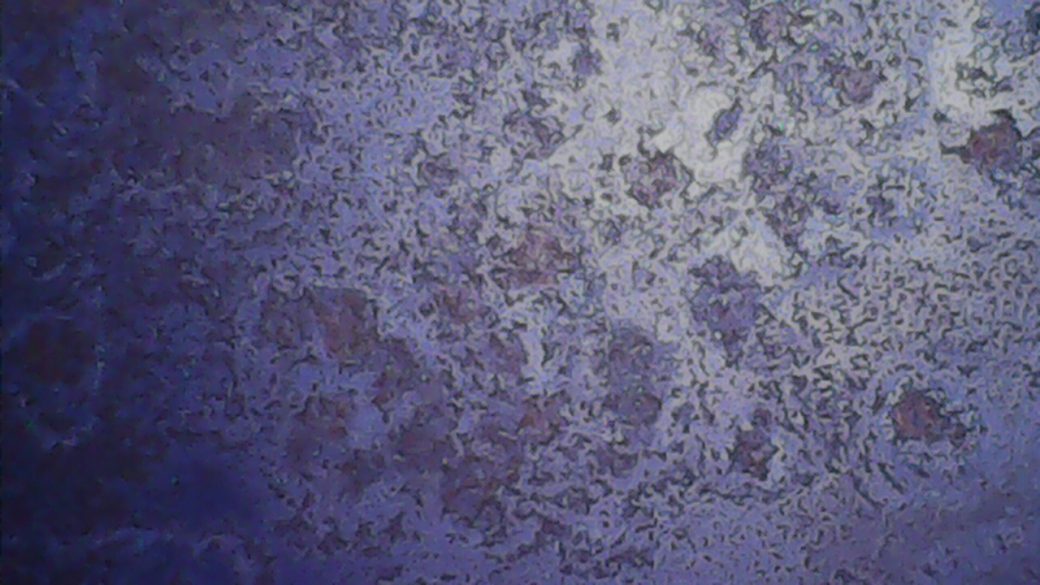
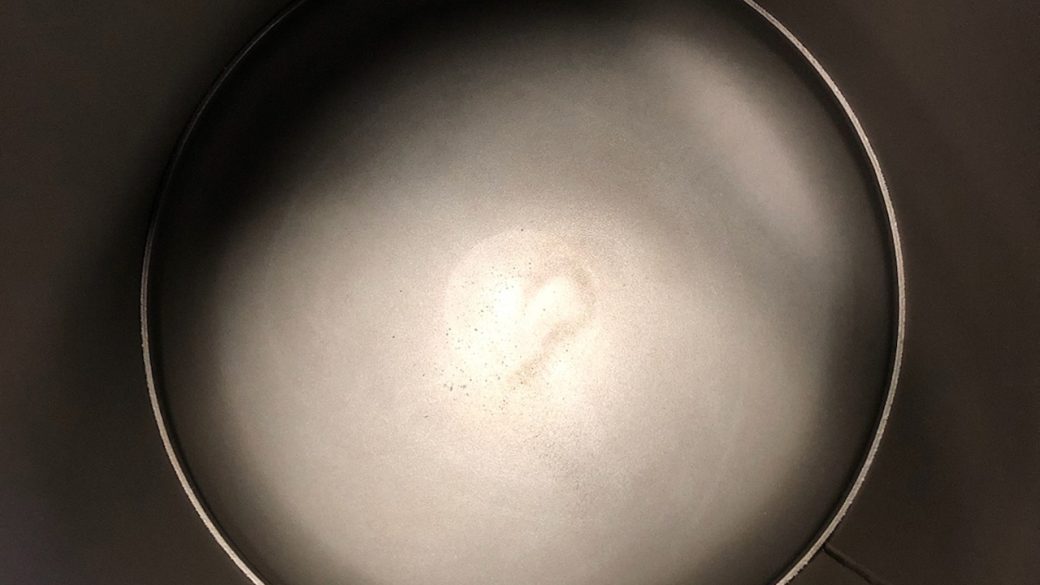
Specialty Valving Procedures
Gas Innovations also implements specialty valving procedures to minimize contamination. Valving is an abrasive process, and multiple de vales and re valves should be avoided. Each time a cylinder is de valved / re valved it can jeopardizes the integrity of the valve threads and introduces metal / debris into the cylinder.
Cylinder / valve preparation
Shown in the table to the right are the metals / contaminants introduced during the industrial valving process.
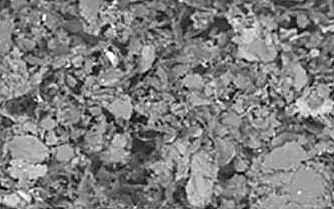
Element | wt% | Suspect Source(s) |
---|---|---|
F | 54% | Thread sealant tape/paste |
C | 34% | Thread sealant tape/paste, weld soot potential, 304L SS |
Fe | 3.2% | 304L SS |
Cu | 1.9% | Brass valve/plug |
Pb | 1.9% | Brass valve/plug |
Cr | 1.1% | 304L SS |
Al | < 1% | Unknown |
Si | < 1% | 304L SS |
Ni | < 1% | 304L SS |
S | < 1% | 304L SS |
Ca | < 1% | Unknown |
Cl | < 1% | Thread sealant tape/paste |
3. Analysis / Traceability
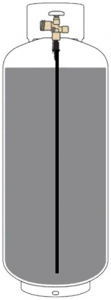
Guaranteed Quality / Traceability. Gas Innovations onsite laboratory uses FID (Flame ionization detector) to certify product at parts per million (PPM). Cylinders are tested after fill to ensure quality. Certificate of conformance (COC) list your cylinders serial #’s ensuring products meets purity standards.
*GI utilizes a dedicated cylinder fleet for high purity solvents. This eliminates cross contamination and unknown impurities that can be introduced from different industrial applications.
Certifications and Analysis
- Expert analytical capabilities.
- Each order is accompanied with a certificate of conformance at no additional charge.
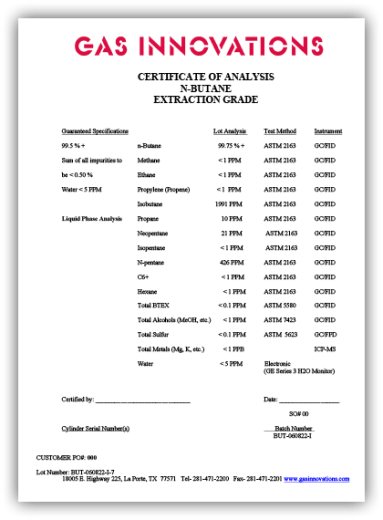
Frequently Asked Questions:
Q: What is top filling a cylinder?
A: Top filling is refilling a cylinder that has not been evacuated, and put under vacuum. Instead gas product is filled right on top of residual product and unknown contaminants. This is common among industrial gas filling operations. See Gas Innovations Refill Procedures above for more information. Top filling into cylinders leads to inconsistent purities, uneven mix ratios and unknown contaminants.
Q: What causes black flakes / particulate in my cylinder?
A: This particulate is left over from the cylinder's manufacturing process. All carbon steel cylinders rust over time and is accelerated in the presents of moisture. These solvents do their job and will dissolve any non-volatile residue (rust) from the cylinder wall. An internal wash can minimize this, along with an in line micron filter. To eliminate particulate and residual oils we would recommend a stainless-steel cylinder as is used in most critical applications.
Q: Why is purity important?
A: The higher purity the product the more consistent the product. Meeting higher purities like 99.5%+ requires removal of impurities and contaminants. Lower purity products vary in purity and can have higher amounts of harmful contaminants ( ex. BTEX, C6+, Hexane, Alcohols & Acetone).
Q: Do I need to distill my products?
A: Gas Innovations products are pre distilled and ready for use. The term “distillation” in the extraction community is more of a “passive distillation” which is filtration. This may remove some solids/ particulate but will not eliminate contaminants with a similar chemical composition (ex. Benzene). Save downtime with GI’s guaranteed pure products.

18005 E. Hwy. 225
La Porte, TX 77571
P.281.471.2200
F.281.471.2201
Sales@GasInnovations.com